Telemetry innovations for gas users and suppliers
February 25, 2021
The gas industry began using telemetry several years ago when suppliers developed technology for monitoring pressure differential in bulk gas systems. Having remote access to information provided great advantages to customers and suppliers, but there has been a hesitancy in some circles to embrace telemetry, perhaps because of unease about costs or technical issues. However, new technologies have been introduced that should alleviate these concerns and motivate widespread acceptance.
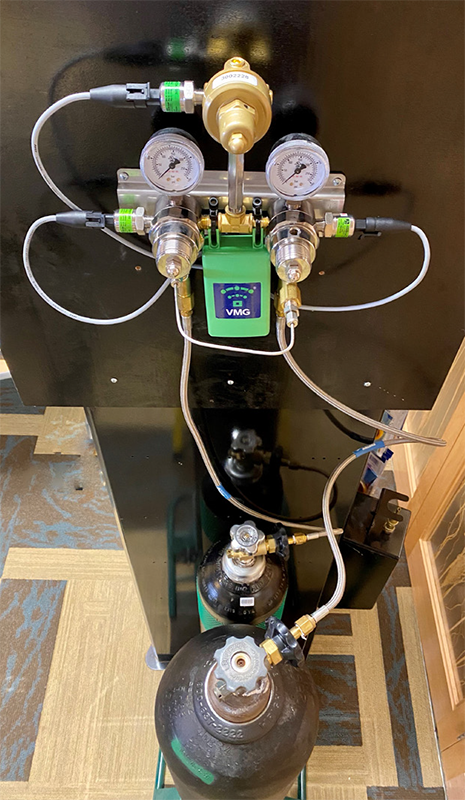
© VMGTM | By monitoring with telemetry, a smaller reserve cylinder can be use
Now telemetry can be used with a growing list of specialty gases, including laser, lab and protocol gases, as well as gases used for welding and fabrication, research, and calibration. There is an expanding interest in how telemetry can be integrated into existing systems and designed into new systems to positively impact operations.
Short-term and long-term benefits
A critical factor for customers is having an adequate supply of gas so they avoid having to shut down operations or lose valuable products. The use of telemetry, however, provides many longer-term benefits to both users and suppliers as it enhances operational efficiencies and effectiveness. Telemetry allows access to real-time and historical data can also improve decision-making and optimize resources. Tools can be customized to provide metrics with the most relevant data and then integrated into Enterprise Resource Planning (ERP) systems.
Telemetry in action
Real-world examples demonstrate the positive impact that telemetry is making for gas suppliers and end users. Here are a few applications where telemetry’s role is contributing to bringing down costs and improving customers’ experiences.
- The research and development department of a major auto manufacturer manages 35 different protocol gases sourced from more than 120 high-pressure cylinders across two buildings and six different locations. VMG designed a system whereby sensors take readings every hour and send radio frequency (RF) signals to collectors which transmit the data to the cloud. Lab technicians and the gas supplier have access to information via dashboards. Hourly readings are tracked on the details page and can be exported for analytical review. Calculations are made using information about supply levels and expiration dates. A customized alert system acts as a failsafe and triggers email notifications based on reaching predetermined levels or change amounts so that gas level certainty is ensured.
- An international specialty metal supplier uses multiple lasers and gases with different configurations for aerospace and other large industrial clients around the world. Workflow and jobs fluctuate, so managing the gas supply can be challenging. Several kinds of shielding gases such as liquid nitrogen, liquid argon and helium, are paired regularly with laser gases such as carbon dioxide, helium and nitrogen. With varying flows and pressures in the lines, it is important to not only monitor the levels of the tanks but also the pressures going to each laser. By putting pressure transducers in the lines and using telemetry, VMG and the supplier have provided monitoring capabilities that will keep the pressure lines stable and troubleshoot equipment problems when the gas usage has an unusual spike.
- Through the use of telemetry, VMG is helping a global consumer packaged goods company focus on its research, maintain FDA compliance and reduce operational costs. The researchers are involved in high-level studies and testing that necessitate precision and protection of its work. Telemetry enables eyes to be kept on gas operations at all times. Since integrating telemetry into its facilities, the company has been able to maintain its high-quality standards while it reduced the number of on-site technicians since much of the monitoring and measurement can now be done remotely without the need for manual checks. Delivery of cylinders can also be delivered as needed, rather than kept on-site.
- Cincinnati Children’s Hospital Medical Center, like most health facilities, relies on nitrogen for their anesthesia, lifts and air tools operating room needs. VMG designed a telemetry system with a redundant backup system that ran in conjunction with the bulk tank, as well as an emergency reserve system, with a bank of 12 more nitrogen cylinders that will provide gas for several more hours. Wright Brothers, the gas supplier, is notified if any of the backup systems are activated. Alerts are sent immediately to ensure there is never downtime in the gas supply. Data provided by the system helps the medical center benchmark performance, forecast for budget and peak usage times, and solve problems. The system proved valuable even from the start, with Wright Brothers utilizing data from the system to diagnose a venting issue and modify safety equipment to address the issue.
What lies ahead
With the latest advancements in technology and lower price options, end users of all sizes should consider taking advantage of telemetry. As previously mentioned, while telemetry has roots in bulk usage, now its use with cylinder and micro bulk applications is very affordable and expanding rapidly. Telemetry systems can be retrofitted with existing equipment or designed for new installations.
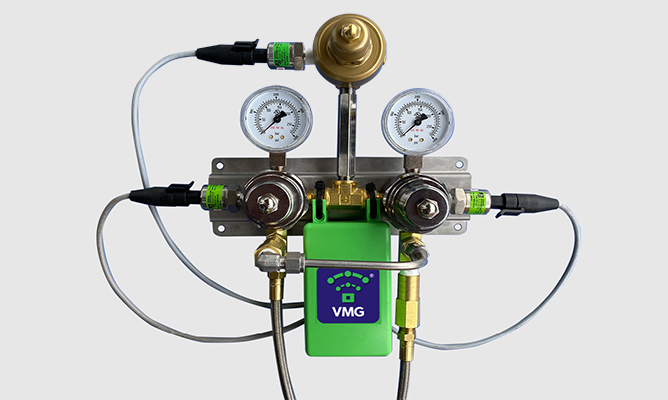
Other recent innovations that are being integrated into use with telemetry are new simplified “smart” switchover manifold systems and also telemetry that monitors for line pressure and flow. VMG’s Automatic Switchover Smart Manifold™ and the just patented Automatic Reserve Fill Smart Manifold™ give the end user and supplier remote notification that the manifold has switched to the reserve as well as the status of the primary and reserve cylinders. With the automatic reserve fill concept, the reserve cylinder can be smaller than the primary cylinder(s) since it is only about providing product until a delivery is made on the primary side of the manifold. This reduces operator error since the same primary cylinder(s) are always replaced. By the reserve cylinder being smaller, the manifold system takes less floor space plus the reserve cylinder is less expensive. The reserve cylinder in many environments could be located in the back of a cabinet totally out of the way. What lies ahead is telemetry-enabled manifolds providing a gas system instead of just gas cylinders.
Telemetry is contributing to the success of the vaccine that is being developed to fight the coronavirus, the cars that we drive, and the food we buy in the grocery stores. The use of telemetry will continue to grow in small and large applications. All end users and suppliers should be taking advantage of telemetry to improve their operations and performance.
ABOUT THE AUTHOR
Mikey Ahrens is the Product Manager for Vendor Managed Gas™ (VMG). A pioneer in the field of telemetry, VMG is an associate company of Wright Brothers, Inc., a successful third-generation industrial gas distributor founded in 1950. www.vmg.us.com